These are general and special purpose steels widely used for a variety of job requirements. Choose from low cost, versatile 1018 ... up to 1117, 1141 all produced with controlled chemistry, toassure greater internal soundness, cleanliness, improved hardening qualities and better machinability.
For maximum machinability, choose screw stock - including 12L14, 12L14 + Te 1214Bi and 1215, or if greater strength is required select medium carbon, direct hardening steels.
LOW CARBON - CASE HARDENING
A36 (HR) — Bars designed for use in structural applications. Minimum physical properties of 36 KSI yield strength and 58 KSI tensile strength. Conforms to ASTM A36.
1018, 1020 (HR, CF) — A low carbon steel with a medium manganese content. Has good hardening properties, fair machinability. Readily brazed and welded. Suitable for shafting and for applications that do not require the greater strength of high carbon and alloy steels. Conforms to ASTM A-108 and AMS 5069. (Not applocable to bars under 2- 15/16 and sizes lighter than 29.34 lbs. per foot.)
1117 (HR, CF) — A low carbon, high manganese steel. Machinability is greatly improved over 1018, and case hardening is deep and uniform, supported by a tough ductile core. Withstands bending, broaching and most deforming without cracking. Conforms to ASTM A-108, AMS 5022 and QQ-S-637.
11L17 (HR, CF) — The addition of .15 to .35% lead to the 1117 analysis provides for even faster machining without changing the excellent case hardening characteristics. Conforms to ASTM A-108 and QQ-S-637.
M1O2O (HR) — A low carbon, general purpose, merchant quality steel, produced to wider carbon and manganese ranges than standard steels. Suitable for forming and welding.
COMPARISON CHART
Est. Min. Mechanical Properties — Based ¾ - 1-¼ on Rd. Bars.
Analysis |
Tensile Strength psi |
Yield Strength psi |
Elong. in 2' |
Red. of Area |
Brinell Hardness |
Machinability Rating + |
1018 1117 11L17 |
64,000 69,000 69,000 |
54,000 58,000 58,000 |
15 15 15 |
40 40 40 |
126 137 137 |
70 90 125 |
|
|
|
|
|
|
|
+1112 = 100.
MEDIUM CARBON — DIRECT HARDENING
1035 (HR) — An intermediate carbon, special quality machinery steel, higher in strength and hardness than low carbon steel. Used for studs, bolts, etc.
1040, 1045 (HR, CF)— Medium carbon steels used when greater strength and hardness is desired in the as-rolled condition. Can be hammer forged and responds to heat treatment. Suitable for flame and induction hardening. Uses include gears, shafts, axles, bolts and studs, machine parts, etc.
M1044 (HR) — merchant quality steel is similar to AISI 1045, but less costly. Contains lesser amounts of manganese (.25/.60); strength and responsiveness to heat treatment are approximately the same.
1050 (CF) — Strain hardened, stress relieved material which offers 100 KSI yield strength. Improved strength over 1045. Conforms to ASTM A311.
1141 (HR, CF) — A medium carbon, special quality, manganese steel with improved machinability and better heat treatment response (surface hardness is deeper and more uniform) than plain carbon steels. Good as-rolled strength and toughness. Uses include gears, shafts, axles, bolts, studs, pins, etc.
11L41 (HR, CF) — Has all the desirable characteristics of 1141 plus greatly superior machinability — due to 0.15%/0.35% leadaddition.
1144 (HR, CF)— Similar to 1141 with slightly higher carbon and sulphur content resulting in superior machinability and improved response to heat treating. Often used for induction hardened parts requiring 55 RC surface.
1144 A311 CL.B (CF)— Steel bars with 100 KSI minimum yield. Capable of flame hardening to 56-60 R.D. for such applications as piston rods. Conforms to ASTM A311.
Stressproof (CF)— High strength without heat treatment. Stress relieved. Readily machinable with minimum distortion. Conforms to ASTM A311.
Fatigue-proof (CF)— Higher strength than Stressproof achieved by mechanical working and thermal treatment. Eliminates need for heat treating and secondary operations (cleaning, straightening, etc.) Readily machinable with low residual stresses.
COMPARISON CHART
Est. Min. Mechanical Properties — Based on ¾ - 1¼ Rd. Bars.
Analysis |
Tensile Strength psi |
Yield Strength psi |
Elong. in 2 |
Red. of Area |
Brinell Hardness |
Machinability Ratingt + |
ASTM A36 |
58,000 |
36,000 |
23 |
21 |
- |
- |
M1020 |
55,000 |
30,000 |
25 |
50 |
111 |
50 |
M1044 |
80,000 |
44,000 |
16 |
40 |
163 |
65 |
1018, 1020 |
58,000 |
32,000 |
25 |
50 |
116 |
52 |
1035 |
72,000 |
39,500 |
18 |
40 |
143 |
65 |
1040 |
76,000 |
42,000 |
18 |
40 |
149 |
63 |
1045 |
82,000 |
45,000 |
16 |
40 |
163 |
56 |
1117 |
62,000 |
34,000 |
23 |
47 |
121 |
85 |
1141 |
94,000 |
51,500 |
15 |
35 |
187 |
65 |
11L41 |
94,000 |
51,500 |
15 |
35 |
187 |
95 |
1144 |
97,000 |
53,000 |
15 |
35 |
197 |
64 |
+AISI 1112 = 100
SCREW STOCK
These are the fastest machining steels for highest production rates on screw machines. Ail are in the low carbon range and can be case hardened. When superior case hardening qualities are required, selection can be made from the low carbon-case hardening steels.
1215 (HR, CF)— Fast cutting steel is the standard screw stock. A resulphurized and rephosphurized steel for typical production runs. Cutting speeds and machining characteristics approach Ledloy 300. Machined finish is smooth and bright. Conforms to ASTM A108 and QQ-S-637.
1214 Bi — A lead-free alternative to 12L14 and 12L14Te or Se. Bismuth in steel acts as internal lubricant, thus reducing cutting forces and minimizing tool wear at same high rates as leaded products. Conforms to ASTM A108.
12L14 (CF) — A lead bearing steel with average machining rates 30% to 40% faster than 1215. Here's a steel that offers inherent ductility combined with finer surface quality. Since 12L14 is an extraordinarily fast machining steel, it has become the favorite for automatic screw machine work. Conforms to ASTM A108 and QQ-S-637.
12L14+ Te and 12L14+ Se (CF)— A leaded tellurium or selenium bearing material which is among our fastest machining steel bars. Increases parts production a minimum of 25% over conventional leaded steel. Finish is excellent and savings in tool life are substantial. Conforms to ASTM A108 and QQ-S-637.
GROUND & POLISHED SHAFTING
Extreme size accuracy, straight ness and concentricityto minimize wearinhighspeedapplications. Turned, ground & polished bars can be machined unsymmetrically, as in key-seating, with minimum distortion because cold drawing strains are not developed. Drawn, ground & polished bars combinethestrengthadvantagesofcold drawn stock with extra accuracy and lustrous finish. Conforms to ASTM A108 and QQ-S-637.
COMPARISON CHART
Est. Min. Mechanical Properties — Based on ¾ - 1½ Rd. Bars.
|
Tensile, psi |
Yield, psi |
1045 TGP |
82,000 |
45,000 |
1141 TGP |
94,000 |
51,500 |
Stressproof DGP |
125,000 |
100,000 |
Fatigue Proof |
140,000 |
125,000 |
1141 DGP . |
105,000 |
88,000 |
1045 DGP |
91,000 |
77,000 |
1215 DGP . |
78,000 |
60,000 |
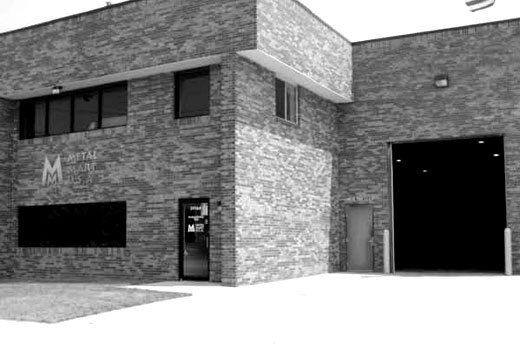
|